The Intersection of Construction Management and Cannabis: Part I
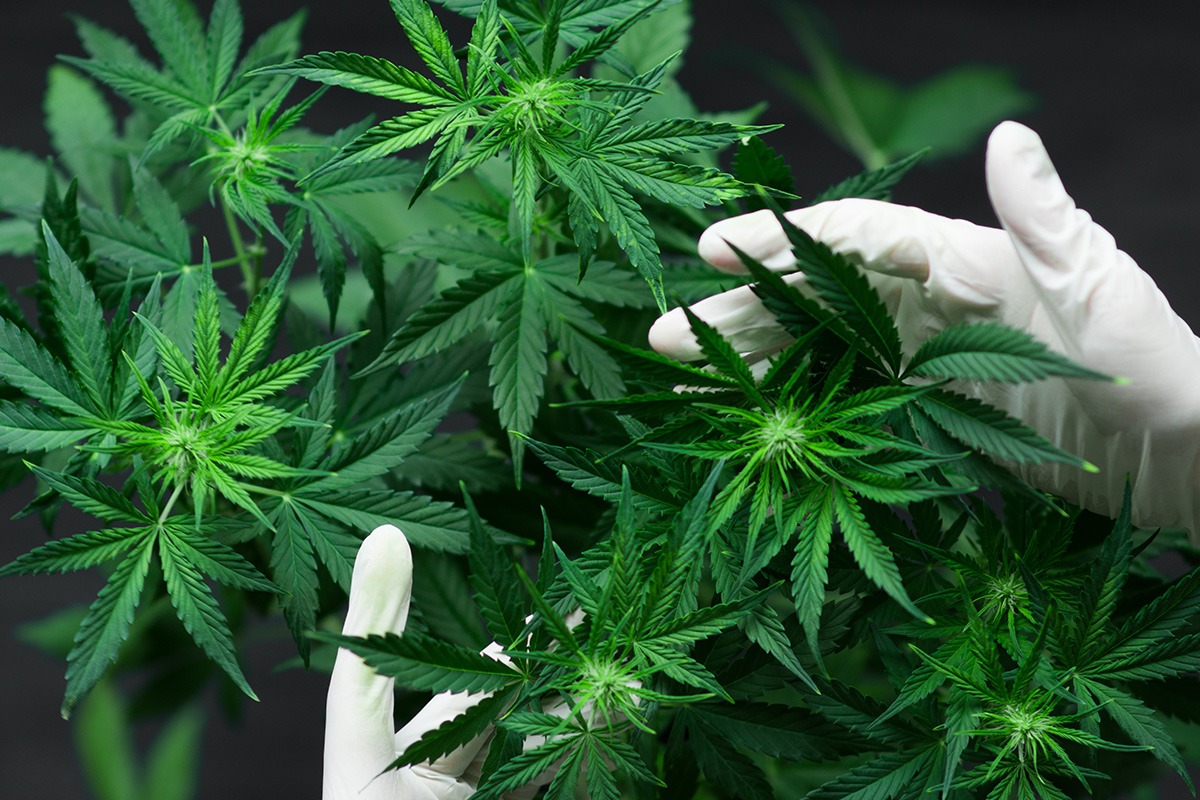
The cannabis industry is ever-booming given increased legalization of medicinal and adult recreational use. The industry’s US market value is expected to reach $30 billion annually by 2025, according to cannabis industry research group New Frontier Data. 36 states and the District of Columbia have approved measures for medicinal cannabis and 15 have approved legislation for adult recreational use. Patient/user sign-ups, sales, and the number of businesses in the industry keep rising.
While cannabis had historically been grown outdoors, the industry shifted to indoor growing and processing leading to higher quality plants and strains through precisely regulated environments. This directly correlates to the need for physical facilities that are well thought-out for production and that meet the extensive local regulations. Consequently, the intersection between the cannabis industry and real estate development and construction demands a marriage of art and science. Real Projectives® has become a leading consultant and project manager for these challenges throughout the United States.
Humidity, temperature, lighting, and airflow play key roles in keeping the plants healthy and producing high quality buds —demanding both botanic knowledge and engineering experience. Cannabis facilities are highly regulated by zoning requirements and many growers occupy existing buildings that were not designed for the heavy utility loads that are required.
Some examples include water leaving the site that might contain high levels of phosphorous and fertilizers that, depending on the AHJ, may need to be filtered out prior to discharge. Most states require recapture and reuse of water used in the cannabis growing process. Designers point out that sloped benching works to control water run-off and recollection. Also controlling humidity and lower the occurrence of excess mildew.
Cultivation operations use a lot of electricity to handle the lighting, dehumidification and cooling requirements, averaging 25-35 watts per square foot. The large amount of HVAC and back-up power equipment needed requires a sound control strategy. Sound barriers can mitigate sound transmission that might otherwise disturb the surrounding area. Similarly, cannabis facilities can produce a significant amount of odor which often needs to be mitigated if the facility is close to other buildings.
Increasingly with the industry’s growth we see more facilities switching from high intensity discharge (HID) to Light Emitting Diode (LED) lighting. While one would be inclined to believe the main reason to the switch would be energy consumption (sodium and metal halide fixtures use significantly more electricity), LED lighting could lead to an increase in yield (ability to stack benches on top of each other), and quality as well due to the ability to control the light wavelengths
Taking just those few elements into account, it’s vital that cannabis growers and processors have a construction project manager that understands and has the experience to make sure all aspects of the facilities are taken into account during design, construction, and startup of new and expanding places. We work hard to stay on top of the frequently changing environment so that we can best inform our clients.
In our next pieces in the series, we’ll delve more into the specifics around dealing with utility issues, integration of furniture and equipment, obtaining inspections, and scaling up multiple cannabis facilities.
Whether you are an investor, developer, or grower of cannabis looking to break into or scale up within this interesting sector, please contact us to discuss how we can leverage our knowledge, expertise, and ambition to drive your next project or portfolio to success.