The Intersection of Cannabis and Construction, Part 2: Utilities
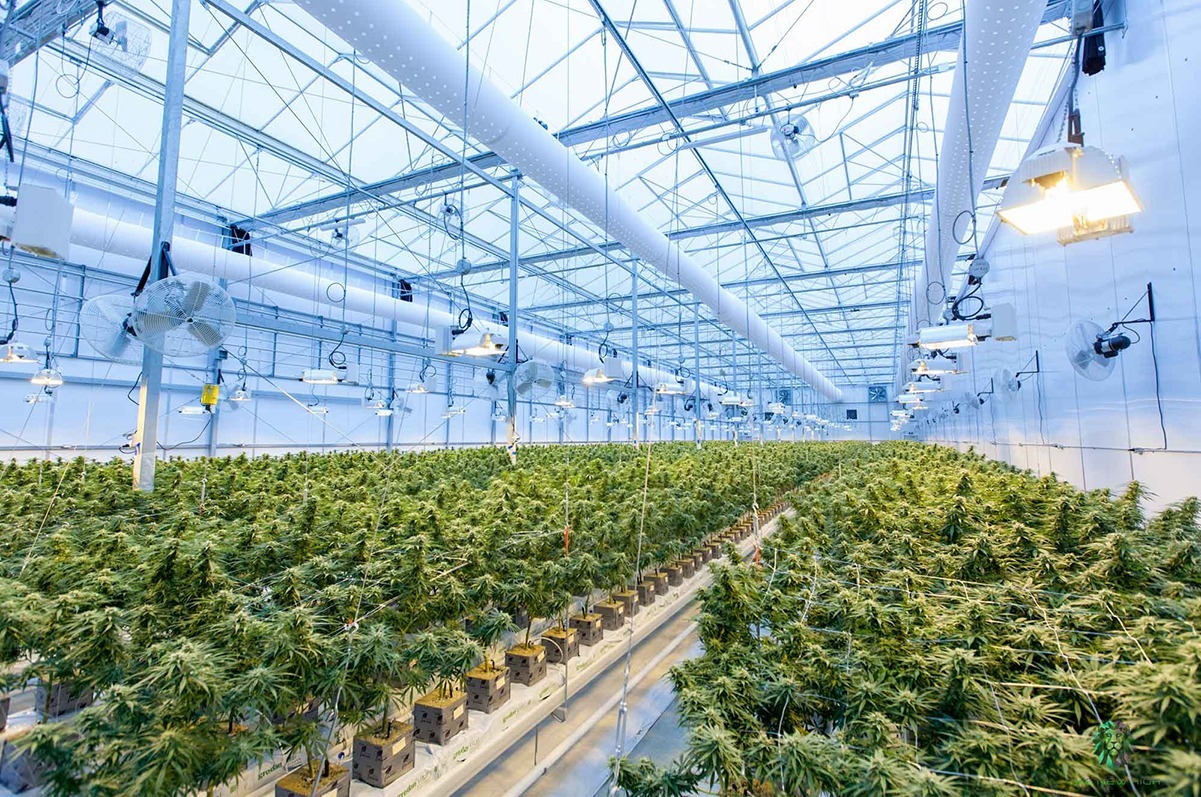
The Intersection of Cannabis and Construction, Part 2: Utilities
Real Projectives® (RPL) drives project results and manages risks for our clients. As such, our experience with more than 40 cannabis cultivation and processing renovations and construction projects throughout the United States has led to deep capabilities regarding the many facets involved in getting them completed. We know that the set up and provisioning of all necessary utilities is an important aspect of opening or enlarging a cannabis facility and should be proactively planned and managed every day of the process.
Early in a project it is essential to identify if, where, and how much capacity of each utility is available when expanding or constructing a cannabis facility. Due to local public sentiment and land values, cannabis cultivation and processing facilities are often located in suburban and rural settings where there may not be any public utilities, so that would require on-site private systems. Adaptive reuse of older industrial buildings is also common and therefore important to understand both the capacity and condition of existing utilities. The owner or project manager should engage an architect, engineer, and sometimes even a contractor, to critically evaluate utility needs and availability prior to signing an agreement to purchase or lease a site, and again during the design phase to make sure the solutions work. As early in the process as possible, engineers should be in contact with respective utility providers any time the services need to be added, replaced, or increased as those steps can take a very long time. Let’s look at a few specific utilities.
Water
Cannabis cultivation facilities may require a considerable amount of water. The consumption, treatment, reuse, and discharge of water are essential design and cost considerations. Large storage tanks for the fertigation system need to be located appropriately to meet the design and structural capacity of the building. In some jurisdictions, condensate and leachate are required to be reclaimed and reused, often being fed back into reverse osmosis (RO) and fertigation systems. As always, coordination early on with the local water authority is key to understanding project specific constraints that may arise from local code and their related impacts to both project cost and schedule. It is also important to compare the new anticipated water consumption to the prior water uses so that the project budget reflects any additional “fixture units” for initial impact and ongoing charges. Successful completion of a project depends on the proactive coordination of the utility company, equipment suppliers, plumbers, electricians, and treatment vendors.
Electrical and Lighting
Cultivation facilities can consume a significant amount of electrical power for operating equipment and simulating daylight. The existing service may not adequately satisfy the needs of the intended building, renovation, or expansion, and therefore must be replaced (sometimes called “heavied up”) that can be a huge hit to both the project cost and schedule, especially during storm seasons when utility companies prioritize keeping existing customers up rather than installing new or replacement services and meters. On top of that, gas- or diesel-powered generators are commonly used as a source of backup power or may even provide the primary power if a site is not located near a public power source.
Additionally, since lighting quantity, quality and time of exposure are essential for indoor cannabis plant growth, the operators require careful engineering and installation of both the right fixtures, monitoring and control systems. Most cultivators now prefer LEDs and sophisticated digital controls to deliver adjustable output, reduced energy consumption and require less cooling and dehumidification that further reduces power consumption. As there are a limited number of lighting suppliers, placing orders early on helps ensure that the fixtures and systems will arrive on time for installation.
Sanitary and Storm Sewer
From our experience, most local jurisdictions have requirements to treat or filter water used in the cannabis facility prior to discharging it from the site. The design team must understand as soon as possible what types of effluent are required to flow into sanitary and what are allowed to go into surface or underground storm water facilities. Since water flows naturally downhill (unless it is pumped up) the depth, size, routing, and location of the existing pipes must be surveyed to ensure that designs of new and extended pipes are able to connect properly, otherwise there can be costly changes during construction. One technique the team should consider is employing video inspection of existing pipes when available drawings and visual inspection do not provide adequate and reliable information. And don’t forget—even if the pipes are adequately sized, the new cannabis use may discharge more effluent to sanitary than the prior uses, so additional impact and discharge fees should be budgeted.
As with most renovation and construction projects, evaluating utilities and proactively coordinating their modification and installation is vital to deliver many cannabis cultivation and processing facilities on time and within budget. RPL goes beyond understanding these issues to assemble appropriate experts, ask relevant questions, and orchestrate the players every step of the way to proactively control costs and drive productive schedules while minimizing unwanted surprises.
In our next articles in the Intersection of Cannabis and Construction series, we’ll delve more into the specifics around dealing with integration of furniture and equipment, obtaining inspections, and scaling up multiple cannabis facilities.
Whether you are an investor, developer, or operator of cannabis facilities looking to break into or scale up within this challenging and growing sector, please contact us to discuss how we can leverage our knowledge, expertise, and ambition to drive your next project or portfolio to success.