Six important elements for Distribution Centers
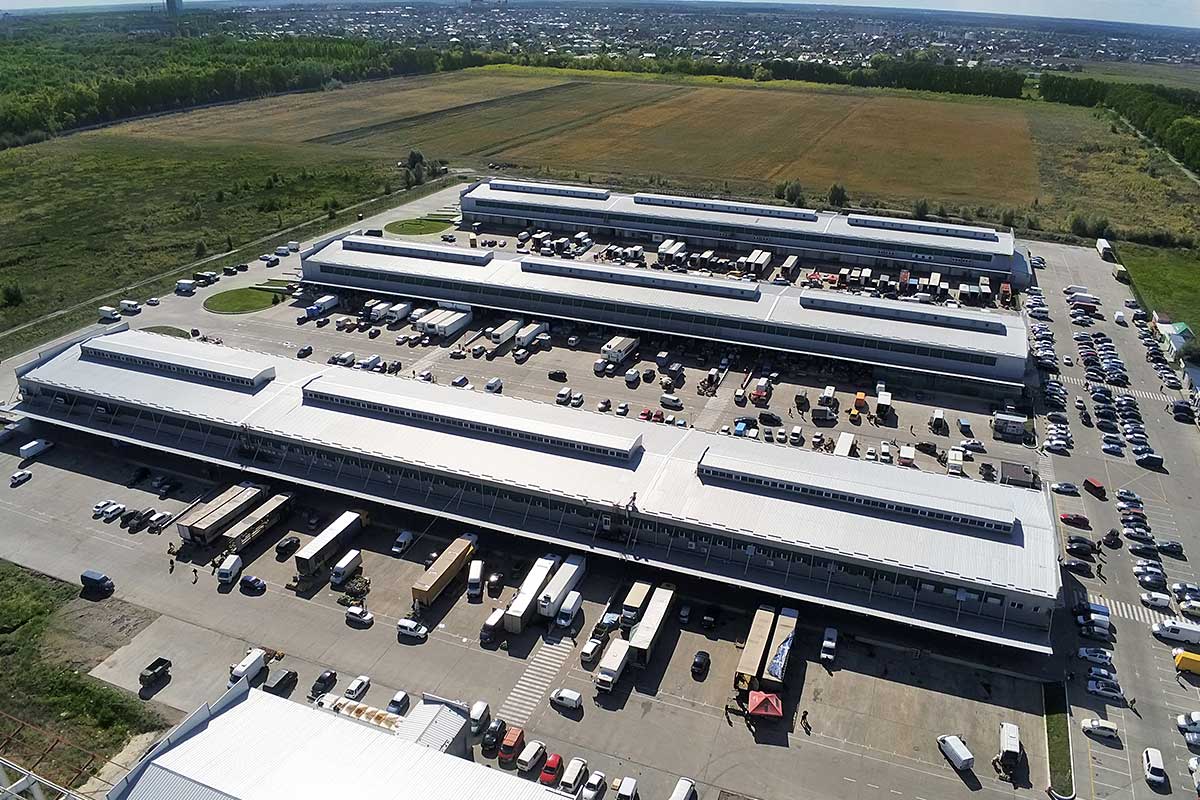
When it comes to the development and construction of warehouse and distribution centers, the Real Projectives® team is adept in evaluating the existing site, planning and budgeting for, and overseeing these projects to completion.
There are many important elements to address when developing or renovating industrial distribution centers and here are our top six examples:
1. Transforming land
Typically, the land for a distribution center encompasses many acres and will not be flat by nature. Dealing with that topology to locate one or more buildings requiring flat concrete floors demands careful thought as moving dirt can be both risky and costly.
2. Water management
Sometimes, industrial sites don’t have reasonably accessible sources of public water or sanitary sewer. This leads to either extending public pipes over long distances or installing private water and sewer treatment plants. Again, with large sites and big roof areas, there is also a need to create multiple storm water management ponds and implement associated storm water best management practices (BMPs).
3. Maneuverability for trucks and trailers
Getting trucks and tractor trailers in, out and around industrial distribution centers safely and efficiently is one of the most important aspects. Engineers study and plan for how the trucks get into and out of the site as well as how they move about while inside the property. Those trucks must be able to back up to loading dock doors where they can load and unload cargo. And it’s also important to build parking spaces to stage empty trailers while they’re not being used.
4. Floors Quality
Modern warehouses and distribution centers depend on clear volume of space that can be 34 feet and taller to the underside of the roofing structure. However, in order to stack boxes and store goods that high, the floors must be incredibly flat and smooth so that tow motors (forklifts) and racking can be kept vertical and level without tipping over. Of course, this is where the underlying grading of the dirt serves as a base for the expansive concrete floors to be placed flat and level.
5. Electrical power
Depending on what kind of product is designated to go through this distribution center, it may be necessary to condition the interior with heating, air conditioning or refrigeration. Regardless, the movement of goods within the building is often accomplished by sophisticated storage and inventory management tracking systems. All these systems have one thing in common they need a lot of electrical power generally at industrial voltages.
6. Resources
Due to the incredible size of distribution centers ranging from 100,000 to over 1 million square feet, it takes a lot of materials and labor to build them. Their roofs are very large so there can be trouble finding enough steel framing, decking and roofing materials, the floors and walls are often made from thousands of cubic yards of concrete, and the electrical gear and generators are custom made and could take up to a year to receive from time of order. Sourcing, contracting and tracking the procurement of materials and labor are essential to completing a distribution center project on time and budget.
If you are thinking about purchasing or enhancing a warehouse or distribution center, please give us a call as we have experience diligencing acquisitions, creating capital plans, and managing salient improvements to millions of square feet of industrial properties throughout the U.S. Contact us today or call us at 888.357.7342 to discuss how leveraging our knowledge, expertise, and ambition could drive your next project or portfolio to success.