Seven Things That Make a Good Guaranteed Maximum Price (GMP), Part 2
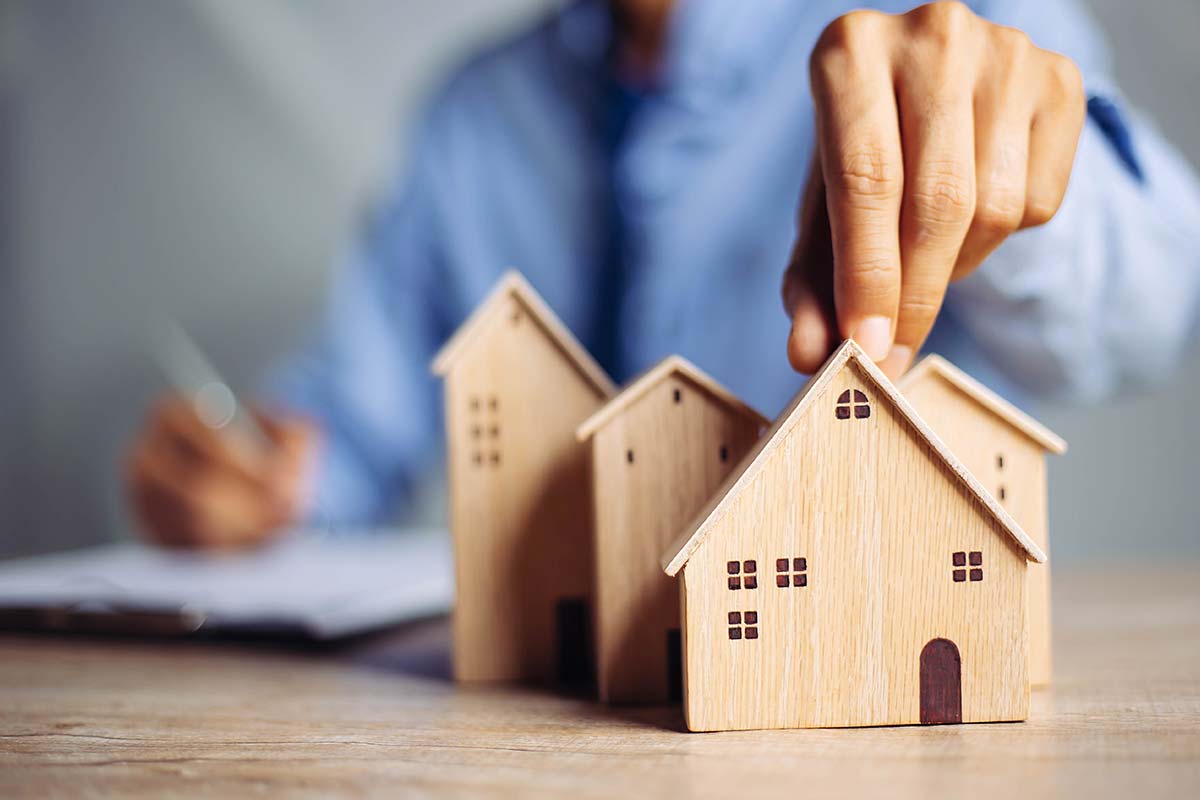
When should you use a GMP and when shouldn’t you? This is the second part of our three-part series discussing GMP’s.
In the first part we discussed what a GMP is. In this article we’ll go into when you SHOULD have a GMP (guaranteed maximum price) in your agreement and what you should include in one.
So, when should a buyer/purchaser use a GMP? The short answer is: Whenever you can! If it’s practical and feasible, you should have a GMP in your cost-plus-fee contract. Establishing the cap transfers a significant portion of the cost control responsibility to the contractor for getting the job done within the budget and therefore protects you and your client (buyers) from many price risks. And often the contractor has stronger relationships and is in a better position than the purchaser to leverage purchasing power. “While we see some contractors balk at GMPs, those we’ve established relationships with are more likely to agree to them, though they might complain about it,” Senior Project Manager Tony Forano said. And properly set, the contractor is still incentivized to bring the work in under the GMP through shared savings provisions.
Assuming that you’ve agreed with your contractor to have a GMP, we suggest paying attention to the following seven things that make a good GMP.
1. Defined scope with reasonable assumptions.
Having a well-defined scope is key to setting a GMP in your contract. And assumptions should reflect what is known and reasonably inferable from the status of reports, documents, and site visits. A reputable and experienced contractor should be able to fill in the smaller gaps with justifiable estimates.
2. Defined timeline with reasonable assumptions.
Knowing your timeline and desired phasing are also key. If you set a specific timeline, your contractor will be able to give you a good idea of how much their services will cost. As we all know, over time there are a lot of things that can become variable, for example prices of materials and labor. And always remember that time often has both calendar and money impacts.
3. Clear descriptions for what is allowed to be a “cost of the work” and what is not.
For you to understand what you will be charged by your contractor, make sure there are clear definitions as to what is considered a part of the cost of work. This will set up additional parameters for how you and your contractor can meet the GMP by the completion of your project. Furthermore, general overhead and administrative expenses of the contractor should be included within their fee instead of cost. Also take time to discuss general requirements and general conditions expenses as well as whether they will be treated as other variable costs of work or considered fixed/stipulated (we usually prefer the latter).
4. Budget that includes appropriate qualifications and a detailed schedule of values (SOV).
A detailed schedule of values broken down by segment/trade should be provided by the contractor to help explain the aggregate GMP amount. Any amounts that are to be treated as allowances or contingencies must be broken out. And a detailed SOV is used to better measure earned work and aid in more timely approving requests for payment as the work is performed.
5. Method for tracking buyout of work and over/under amounts to baseline budget.
Combined with a good SOV, it is important to outline how the contractor is supposed to report and track work as it is subcontracted (bought out). And as each SOV line item is bought out, the over/under should be reported.
6. Method for reallocating amounts between budget line items.
When creating your GMP contract, include a method for reallocating amounts between budget line items. This gives you a level of flexibility since some materials (or labor) could cost less or more than you expected. If one cost less than was initially estimated, you can use the leftover funds to accommodate another line item that ended up costing more. This helps you and your contractor meet your GMP. For instance, it is customary for the contractor to be able to use savings in one line to offset overage on another line (reallocation) directly. And while frequently contractors like to sweep the net savings/overages into the contract Contingency line item, we prefer to track them as a separate amount.
7. Formula and timing for sharing savings between owner and contractor.
While Contingency is traditionally returned 100% to the owner, costs that are less than the GMP and left over at the substantial completion of your project, amount to savings that are typically split between purchaser and contractor (e.g., 70% owner and 30% contractor).
Tracking a shared savings account is the best way to know what that amount is and enables simple math to calculate the split and issue a respective change order to the contract. Another essential part to define is when this adjustment made. Many contracts are silent on this matter, and it creates confusion when the owner might want to use the savings to pay for other work while the contractor wants to keep the savings for any surprises through completion. We recommend that a portion of the shared savings be split upon 95% buyout of the work and remaining amounts split upon substantial completion of the work. And watch out for using the shared savings for contractor mistakes near the end of the project as that’s not what the shared savings is supposed to be used for – consider a contractor contingency instead.
In our third and final blog post of this series, we will discuss some examples of when you’re better off NOT pressing for a GMP in your contract.
If you’re planning a new real estate development or renovation construction project, we’d love to discuss the risks and options to help you overcome some of the challenges, like which contract approach to take. Contact us today or call us at 888.357.7342 to discuss how leveraging our knowledge, expertise, and ambition could drive your next project or portfolio to success.