Modular Construction…Revisited: Part I
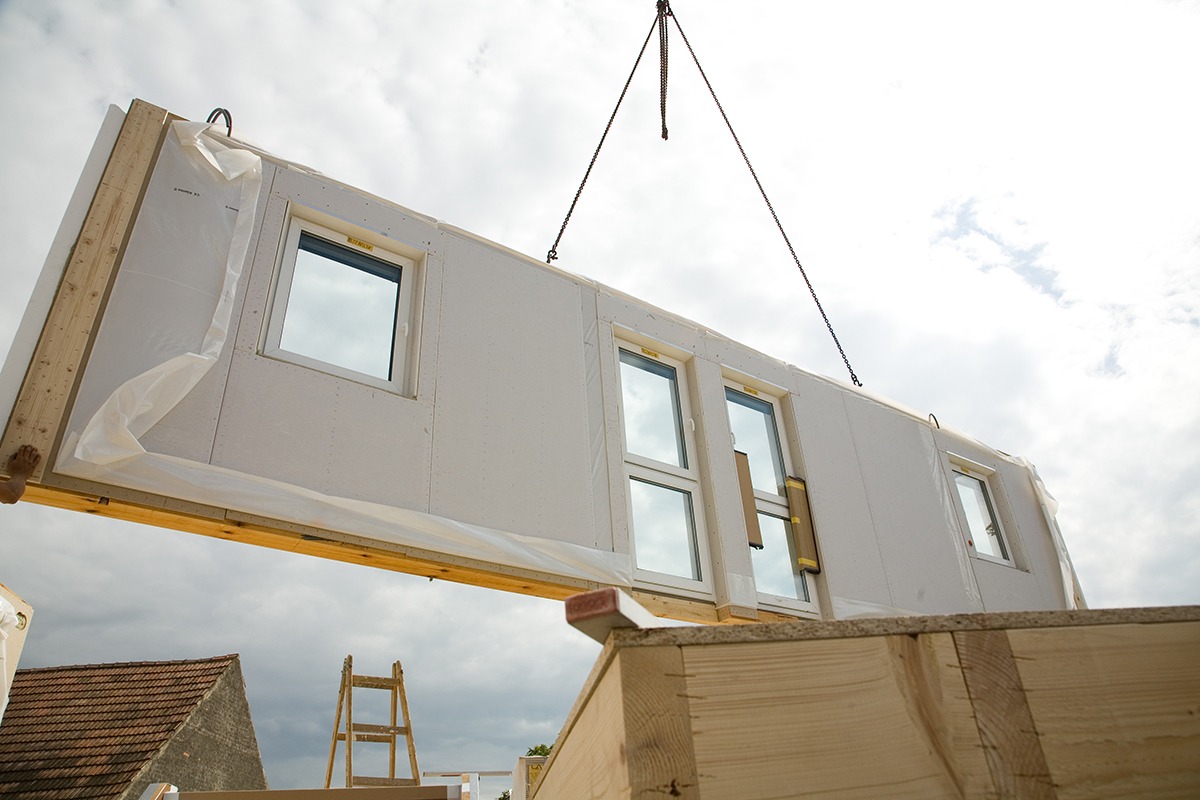
In response to supply chain challenges and labor shortages from local to international scale, the trend toward building more real estate projects away from the project site continues to accelerate, particularly in the use of modular off-site construction. The modular market shows great potential for investors with global growth expected to reach $114.78 billion by 2028 while exhibiting a compounded annual growth rate of 6.1% between 2021 and 2028, according to a 2021 report from Fortune Business Insights. The report put the market at $70.44 billion as of 2020.
For the past three years existing fabricators and many new players have opened and expanded their production facilities across the U.S. and international markets. There’s plenty of room for growth in the U.S. According to McKinsey, modular construction only has about 4% US market share compared to stronger activity in Europe. For example, in Scandinavia it has about 45% market share and 14% in Japan.
Real Projectives® (RPL) has seen this trend firsthand having been involved in multiple projects throughout the United States using significant modular approaches. If you’re contemplating the modular approach in whole or in part on your next real estate project, we’d like to share some advantages and challenges to help you make smart decisions so your project can be completed successfully.
What is Modular Construction?
For centuries, traditional construction brought all the raw materials—like 2x4s and flooring— to the building site for tradespeople to cut and assemble at the project location. With off-site construction in general, and with modular construction specifically, large portions of the project are fabricated away from the job site and within factory-like environments.
It’s important to clarify that modular construction is really a construction method (procurement and delivery approach) rather than a unique real estate product type like some people and media seem to mistakenly classify it. Modular construction is the process in which quality materials are purchased in bulk and fabricated, using some level of automation by trained workers within controlled working conditions, to create a portion of or an entire building.
Some modular manufacturers use stick-building (think 2x4s) techniques similar to traditional construction only within their factory “barns” while others use more advanced assembly lines, and the most modern use automatic equipment and robots. Several are starting to even pre-purchase smaller modules (think bathroom units) incorporating them into larger and more comprehensive modules. The “boxes” leaving the factory can be three-dimensional (3-D) structures with floor, walls, and ceiling—making them volumetric modular. Each box has most of the interior finishes and fixtures pre-installed.
Completed modules are prepared for shipping and transported typically by truck or boat to a staging yard or delivered directly to the project site. Then each module is unloaded and placed (set) to assemble a significantly completed building. For example, on a development project we worked on in Philadelphia, designers and contractors fabricated over 100 modules in an out-of-state factory about 500 miles away, trucked them one-by-one into the city where they were staged at a temporary yard, and later stacked them on top of each other, completing a seven-story apartment building.
Although you may read or hear others describe modular construction as a “new” or “modern” wave, the truth is that modular construction has been used for decades in multiple industries from single family homes to ships and airplanes. More recently, it’s gotten press for the expanded application to multi-family (apartments), hotel, commercial, and industrial use types.
Advantages of Modular Construction
1. Saves Time
Manufacturers tout cutting construction schedules in half or even as much as 75% compared to traditional methods. While we agree that modular construction can save time, those claims often focus only on the site construction period only without looking at the entire project schedule including engineering, material procurement, fabrication, site preparation, transport, erection, and necessary on-site connections and finishes to deliver a completed project ready for use and occupancy. We believe the real potential time savings is more fairly in the zero to 30-percent range of the overall schedule through a modular approach.
2. Higher Quality
Since more work is performed within controlled indoor environments using some level of automation techniques, there are real opportunities to create better quality products. Of course, the level of quality depends on the selection of similar materials and installing them with skilled craftspeople and/or computer-controlled equipment. As the interior finishes such as drywall, flooring and fixtures are frequently done in the factory as well that can beat field-installed work. Two areas where the industry does struggle in this regard is preventing drywall from cracking during transport and lifting and not being able to apply both interior and exterior finishes across the joints where the boxes meet each other.
3. Minimized Weather Delays
By fabricating the modules inside, worries about wind, rain, snow, heat, and cold delaying construction of the modular units is virtually eliminated. It also provides workers safer and more comfortable conditions to be more productive and produce a higher quality product. Also, the modules arrive on-site usually outfitted with flooring, cabinets, counters, plumbing and electrical fixtures, and appliances, thereby needing little effort and time to be ready for use.
4. Improved Site Logistics and Safety
Another advantage of modular construction involves storage of materials on site. When a project site is tight on space, for instance in compact urban settings, the unloading, staging, and moving of materials around the site is difficult and can absorb significant labor and resources to plan and properly manage site logistics. If not done well that causes clutter, slows down work, creates theft concerns, and costs money. By shifting many of that bulk and production to a more spacious and well-organized factory to produce completed modules, construction sites can remain cleaner, safer, and more secure.
5. Lower Labor Costs
An important and potentially controversial advantage involves economics of labor. Skilled labor is in short supply for construction in most places and labor is often very expensive in cities for a variety of reasons. This leads to real challenges when trying to get a building constructed for a given budget and timeline. Modular facilities train workers and allow them to remain in fixed locations (better quality of life with their families) with controlled and safer conditions as mentioned. Those plants can be located to attract those competitive workers and take advantage of important access to raw materials and logistic connections, like highways and rail lines, common in other industries, such as automotive and technology products. Savings on labor varies widely and typically accounts for almost two-thirds of the construction cost, leading to savings up to 25 percent on construction costs.
6. Less Construction Waste
According to a recent UK study, up to a 90 percent reduction in waste materials (think cut off scraps and theft) is achieveable with modular building. With the environment and green concerns becoming more of a focus in the real estate and construction industries, off-site and modular strategies can reduce and eliminate significant amounts of waste on each project. There are efforts to maximize recycling within factories that put the building portions together including using some waste products for cogeneration of electricity and heat.
In the second article on modular construction, we’ll discuss some of the unique challenges and measures you can take to better manage this approach for your project.
If you’re planning a new real estate development or modular construction project, we’d love to discuss the risks and options to help you overcome some of the challenges. Contact us today or call us at 888.357.7342 to discuss how leveraging our knowledge, expertise, and ambition could drive your next project or portfolio to success.