Modular Apartment Construction Accelerates
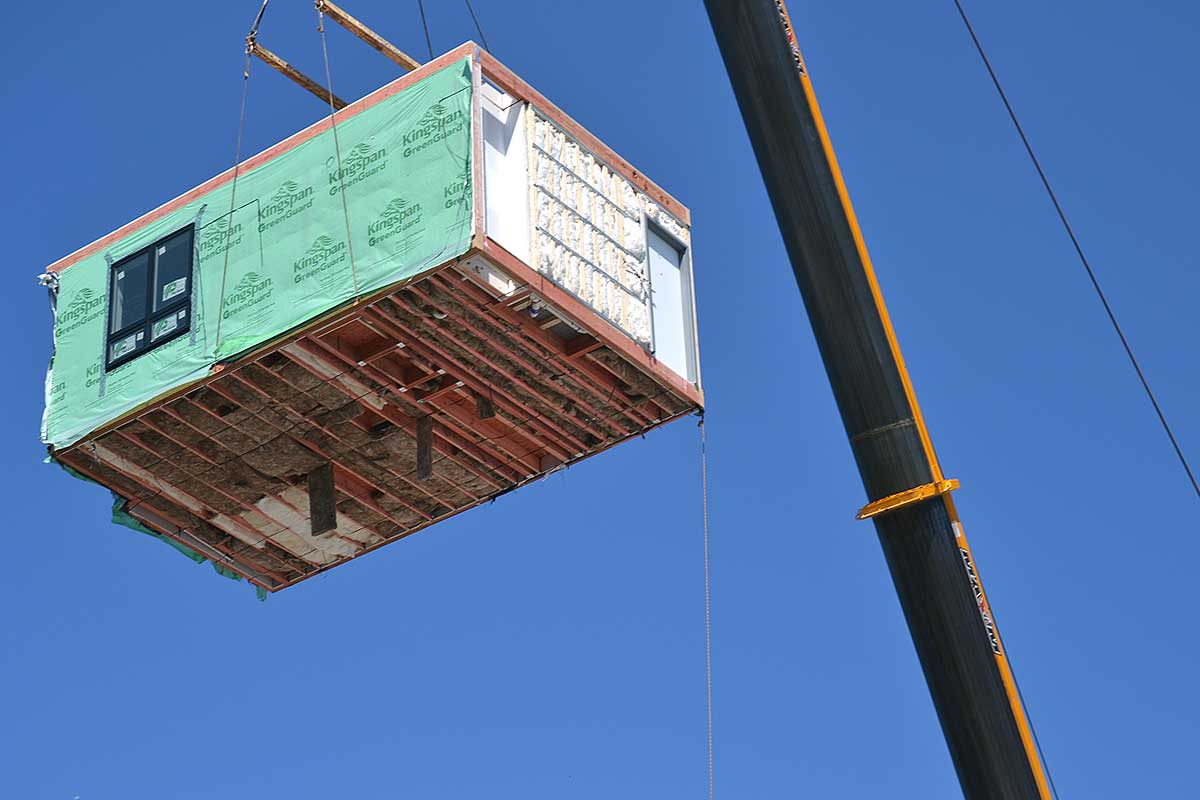
While not a new, real estate developers and investors continue to be intrigued by the growing use of modular construction.
Modular, as one form among a broader category called “off-site” construction is an accelerating force in trying to produce more affordable urban apartments, as seen in our recent six-level project at 4125 Chestnut Street in Philadelphia and is striving to greater heights like 461 Dean in Brooklyn that opened in 2016.
Modular construction is gaining practical and financial traction in portions of the United States (US), after finding much popularity in Europe, and is expected to reach a global market of $130 billion by 2030, according to the consulting group McKinsey and Company. This market offers developers and investors certain advantages not found in traditional construction; elements that lend themselves to our current moment in time.
First and foremost, developers and investors can save time and money. Development of modular elements off-site in a factory-like setting takes away the factor of costly weather delays. McKinsey and Company reports that modular construction can decrease construction time (on-site) by as much as 50%. Additionally, factory production lowers the amount of waste, creating a more cost-effective process. Further savings are achieved with the costs that are lower at the factory than at the typically urban location of the job site. And modular construction provides more control, less waste, and more environmentally friendly processes.
Challenges Remain
There are some challenges with modular construction not found in traditional construction. The front-load funding schedule involved with modular construction takes thoughtful planning. Most of the funds for a project need to be put up early to cover simultaneous payments for planning, engineering, materials, site prep, construction of modules, and payment for the module’s finishes. All of this can make getting loans a little more challenging as many lenders are either not experienced or think of modular construction as something that’s new, when it’s actually been around in the US since the 1800s. People even bought modular home kits from the Sears, Roebuck catalog starting around 1908 and manufactured housing (i.e., mobile homes) are produced in great quantities.
Most well-known module manufacturers have pay-as-you-go structures even requiring as much as 50% paid up front, as well as more frequent pacing than the traditional once a month draw. The more you work with your team to anticipate funding, the better you can manage the process overall. These provisions should be clearly discussed with both equity and debt partners and memorialize procedures within respective agreements as a mismatch can cause tremendous frustration and potentially significant problems during construction.
Another issue for some, is the transportation of module elements from the factory to the work site. While this does offer some risks, transporting modules from a factory many miles from the job site, it’s important to work with hi-quality transporters and riggers, and for them to carefully manage, and be responsible and insured for the transportation of often dozens of loads to the job site. Just-in-time delivery is dangerous. If one faces challenging terrain, tight bridge or road conditions and especially delivery into urban settings where there are often limits to when and how large objects are moved. In order to mitigate shipping risks, we recommend if there is not enough space on the actual job site, that a staging site be arranged nearby to hold at least a couple of days’ worth of boxes to be set, so that any hiccups in transportation do not translate to immediate delays to the crucial erection days.
While some bemoan the standardization in modular construction, modern day technologies are leading to better design and more creative uses of wood, metal, and concrete materials all to allow for other than boring, stacked rectangular boxes. And while apartment design can demand duplicative symmetry even across floor plans and efficiency of operation, today’s modular buildings can offer some variation and creative exploration within those restrictions. And as the industry evolves, even greater advances and efficiencies will be made. From the much more efficient building materials, windows, chilling systems, and other components becoming more environmentally friendly as time moves forward.
What’s this mean for Real Estate Developers and Investors
We are proponents of, and believe that, modular (and other forms of off-site construction) offers expanded opportunities, lower costs, great value, quicker to market results, and potentially better returns for apartment development. We’ve seen solid success with our first Philadelphia project and are currently overseeing a second one down the street.
However, it is important for apartment developers and investors to think about modular as a method of construction and not a separate project type. There have been several meaningful failures and lawsuits on projects not well thought out. So, teams must be diligent about numerous significant differences along with the potential risks and challenges of execution. The industry is still learning and adapting techniques and tools historically used for single-family homes to apply effectively on larger and more customized multi-family builds.
Real Projectives® can help manage any type of construction project, including the nuances of modular building construction, to bring exceptional results. Call us at 888.357.7342 to find out more.