Budget and Schedule: A Wholistic Approach in Challenging Times
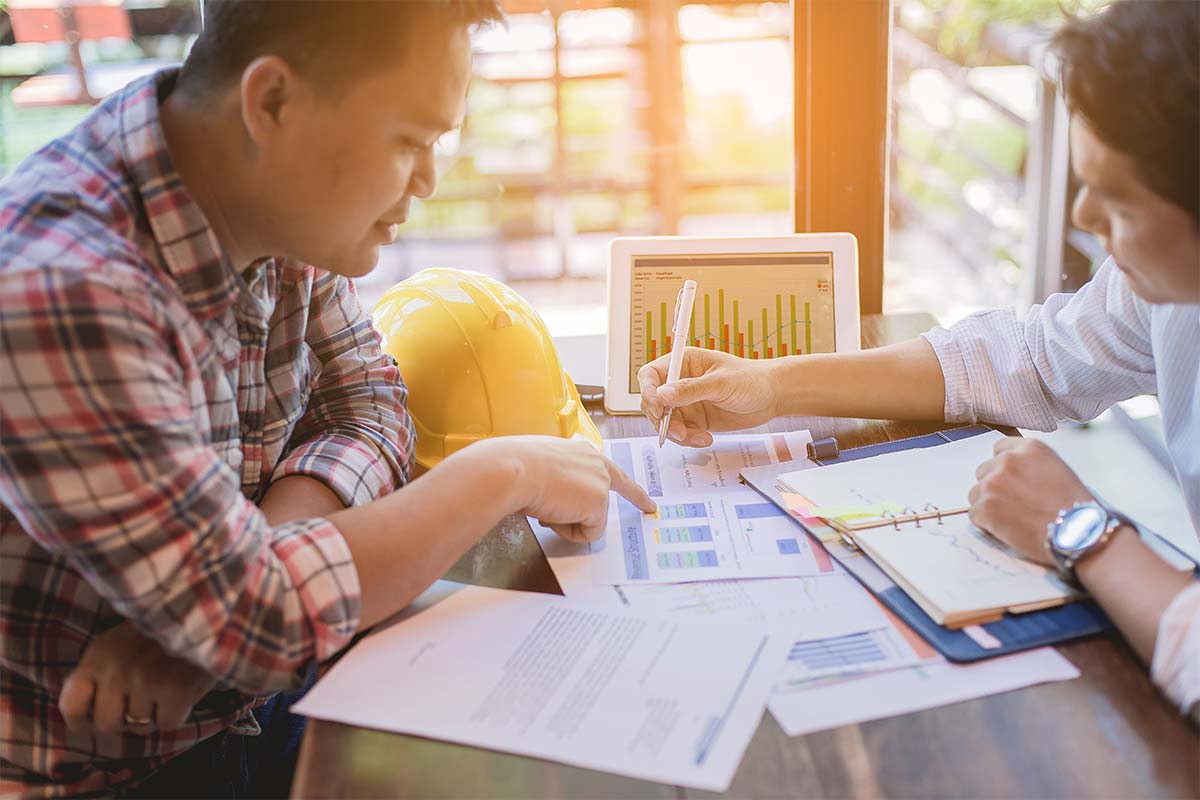
As we move closer toward a full reopening of the economy, we still see issues in the supply chain that may affect construction schedules.
This is highlighted in a recent SouthBmore.Com article about a local developer working on a project in the Pigtown neighborhood of Baltimore City. The publication reported, “He said material costs are currently very high due to demand in the supply chain, and that he will wait to start construction until things come back down to normal….”
What is “normal?” With current market trends and what we are seeing from projects across the country, “normal” will not mean pre-pandemic level costs. Rather we expect costs to reach a more reasonable level than what’s currently being experienced. Overall, we expect prices will remain higher than last year by a fair margin.
The construction industry certainly faces challenges in 2021. According to the Associated General Contractors of America (AGCA) there’s been a dramatic, never before seen, increase in the price of construction goods, delivered in the government’s Producer-Price Index, and compounded by challenges in the supply chain. As of April 2021, according to Random Lengths in Forbes, lumber prices are up 193% since 2020. And according to Metal Miner, the US HRC three-month price rose 20% month over month to $1,280 per short ton. Steel prices have flattened out thus far in April. In any case, these two commodities drive the costs of most projects, and the ultimate decision if a project can move forward.
Ken Simonson, AGCA’s chief economist, echoed these sentiments in an online article from Construction Executive. “While construction has remained one of the economic bright spots during the pandemic, supply-chain problems threaten to derail that momentum as many companies are reporting that projects have been either delayed or canceled…”
As project managers, it’s our role to drive results and manage your risk. We take an overall look at the scope of the project, the timeline, and the budget. And occasionally we need to really help clients weigh the impact of supply chain issues on that timeline and budget of a project. We take a wholistic approach to each project, knowing that each situation is unique and there are implications of different scenarios that must be taken in:
1. Impact to schedule;
2. Impact to cost;
3. Impact to finish level if value engineering is pursued to help offset costs.
We help look at the project schedule and we pull backwards to determine when critical decisions have to be made without adverse impacts to the project, including early release of some elements to limit our client’s cost/schedule exposure.
Our experience, and the relationships we’ve built over the years play a role in getting the job done. We provide clients with a sense of security knowing that we can get them what they need. Occasionally, while we have a variety of contingencies, we may decide that based on availability to go with a higher-priced vendor we know can deliver the goods, rather than rely on the lower priced provider who may not be able to access the product as quickly and as effectively. We plan for these contingencies in the budget and believe it’s more beneficial in the long run, as delays in the timeline usually result in even higher costs. Particularly when planning a timeframe that may be months out from actual start of construction.
Whether you are an investor or developer looking for guidance, please contact us to discuss how we can leverage our knowledge, expertise, and ambition to drive your next project or portfolio to success.